The word ‘Batik’ which translates to wax writing is a form of wax resist dyeing of fabric. Even though the exact point of origin of Batik is still undiscovered, the history can be traced back to two thousand years ago in countries like India, Indonesia and Japan amongst others. While it also spread to Sri Lanka, Malaysia, Thailand and countries in the West, the designs and methods of printing varies from region to region.
Amidst the lanes of the busy city of Ujjain is a small village: Bherugarh. The place is know for the Bherugarh Jail, Kaal Bhairav temple and the production and market of the age old craft of Batik prints.
According to the Madhya Pradesh government, today around 800 men and women from Bherugarh are involved in this craft of Batik Printing. During my short span of visit I could guage that the art has been existing in the lanes of Ujjain since more than 70-80 years now. What started off with just 10-20 karkhanas has now increased to a production supported by 70-80 karkhanas. The art was founded in Bherugarh by Rahim Gutti, a native of the place who is a renowned artist from Madhya Pradesh.
While the cloth is procured from South India (Tamil Nadu), wax from China and the dye from Gujarat, the skill and culture of the people of Bherugarh who still take forward this art form is what binds all these together. In this blog I take you through the dyeing and printing process practiced in Bherugarh through the capacities of my camera and my lenses.
Bleaching
The first and foremost process after procuring the cloth involves measuring and rolling it. These cloth rolls are then be bleached and dried. The cloth is bleached to ensure that the colour used to dye remains intact. While measuring and creating the rolls as well as drying post bleaching is a manual process, the bleaching process is mechanised.
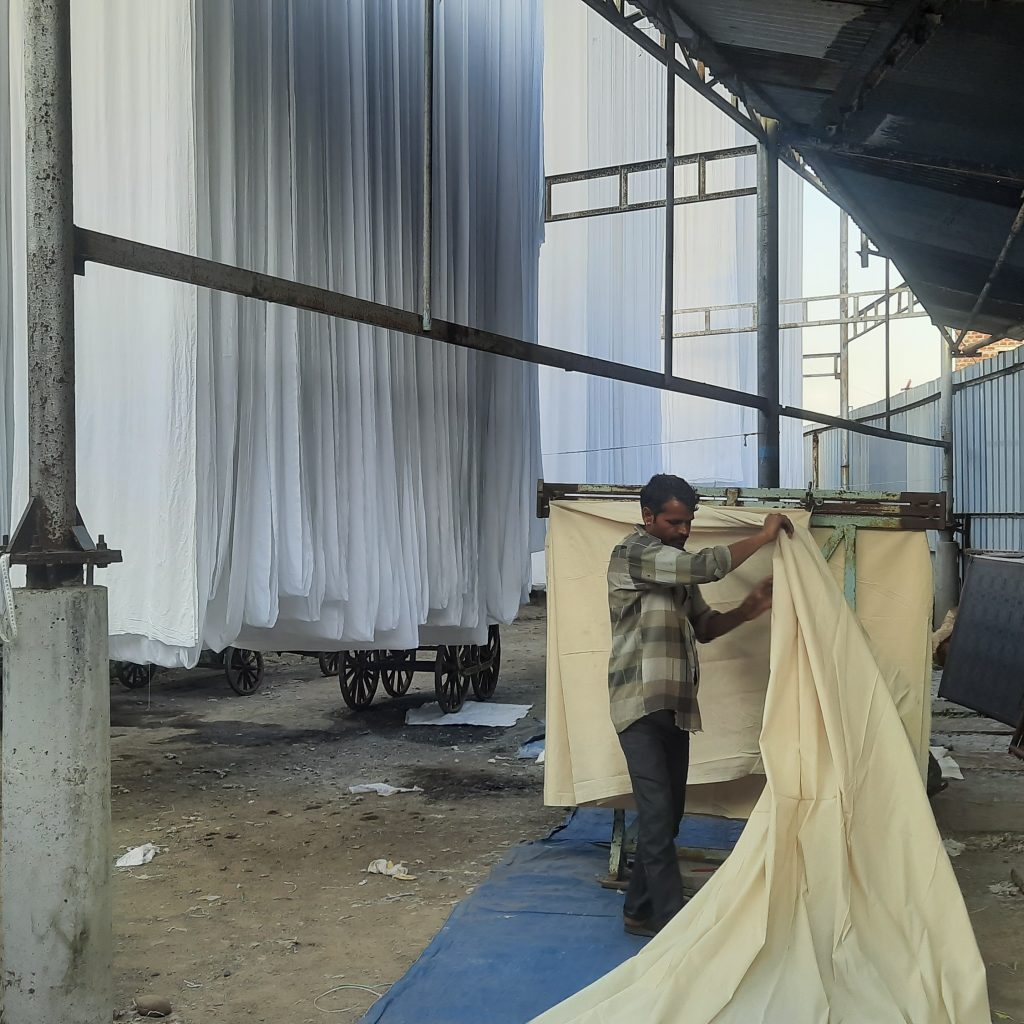
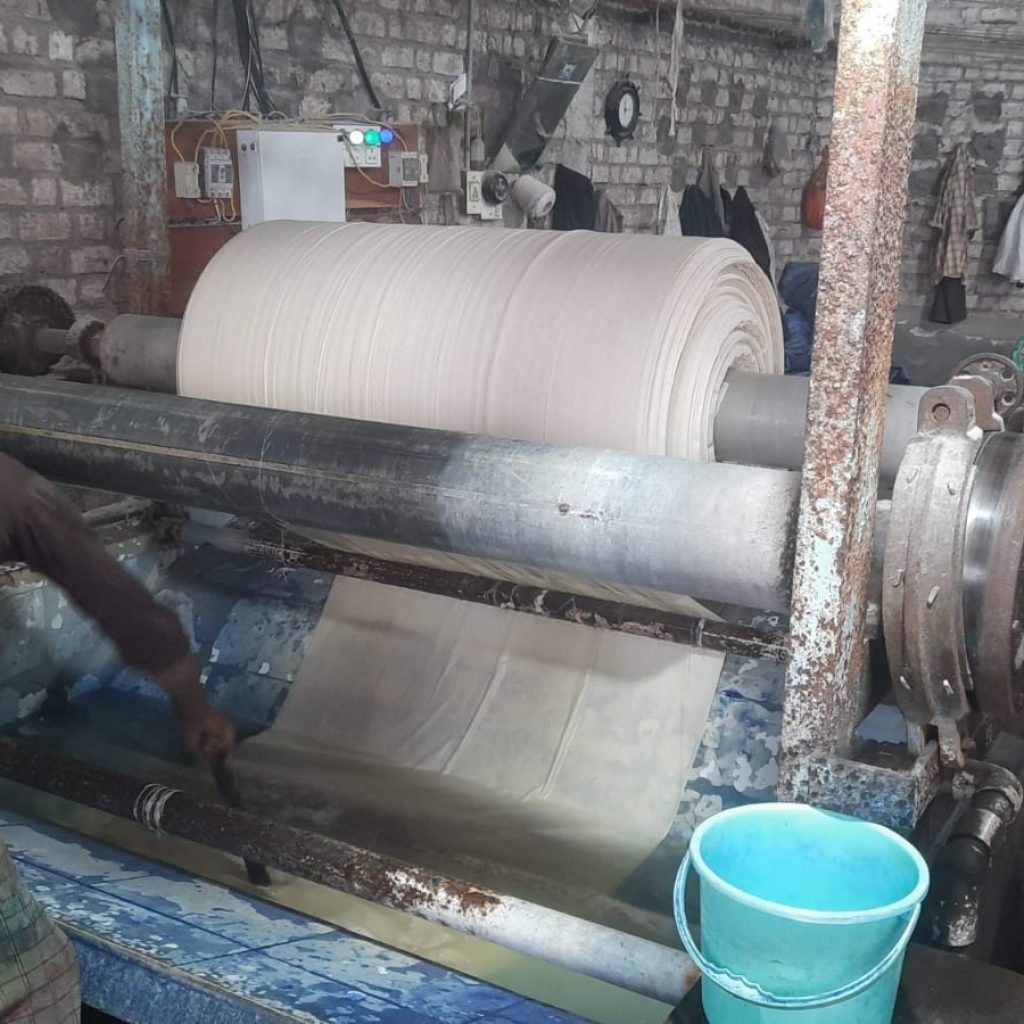
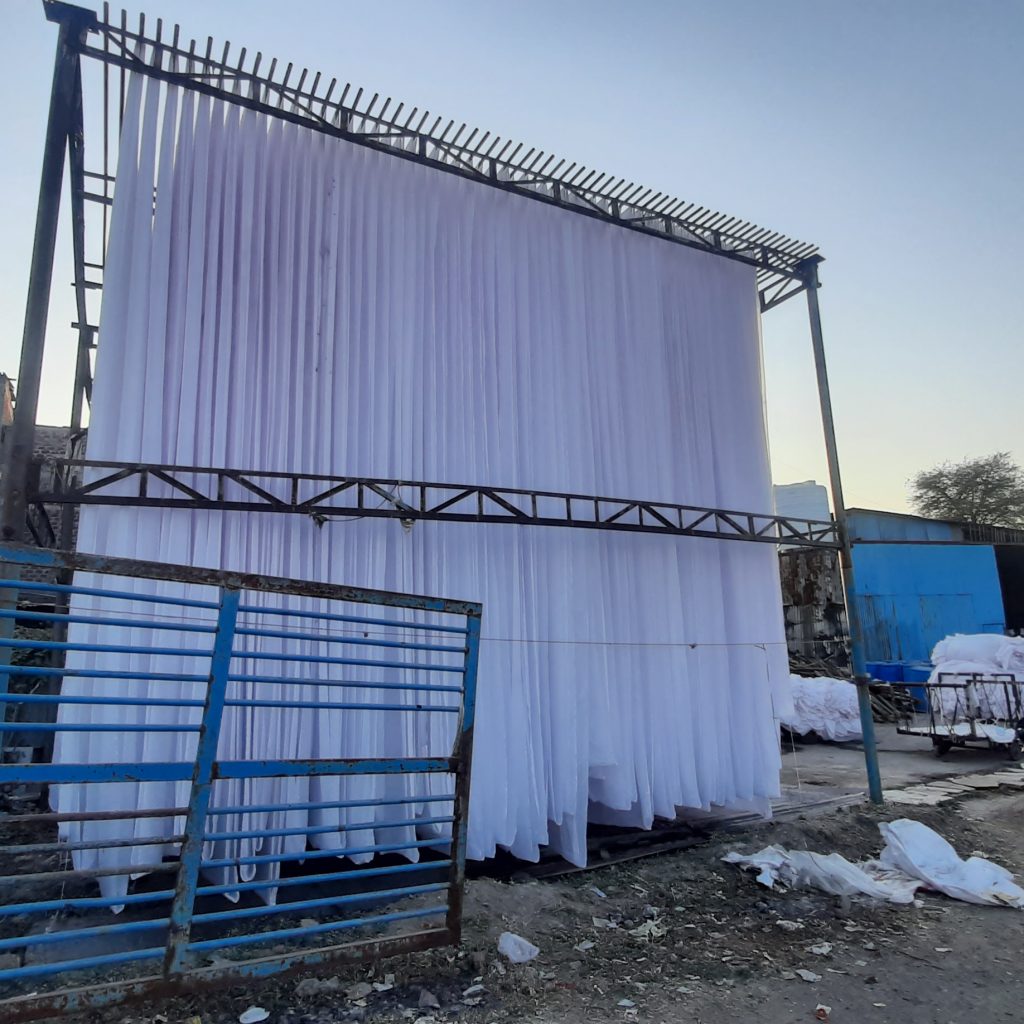
Waxing
This part of the process is one that requires extreme precision and calculation. From maintaining the heat levels of the molten wax to ensuring that the blocks get printed at equal distance, the work which happens here requires extreme talent and expertise. It is interesting how the craft has given space for contemporary modification to use metal blocks in addition to the age old tradition of using wooden blocks.
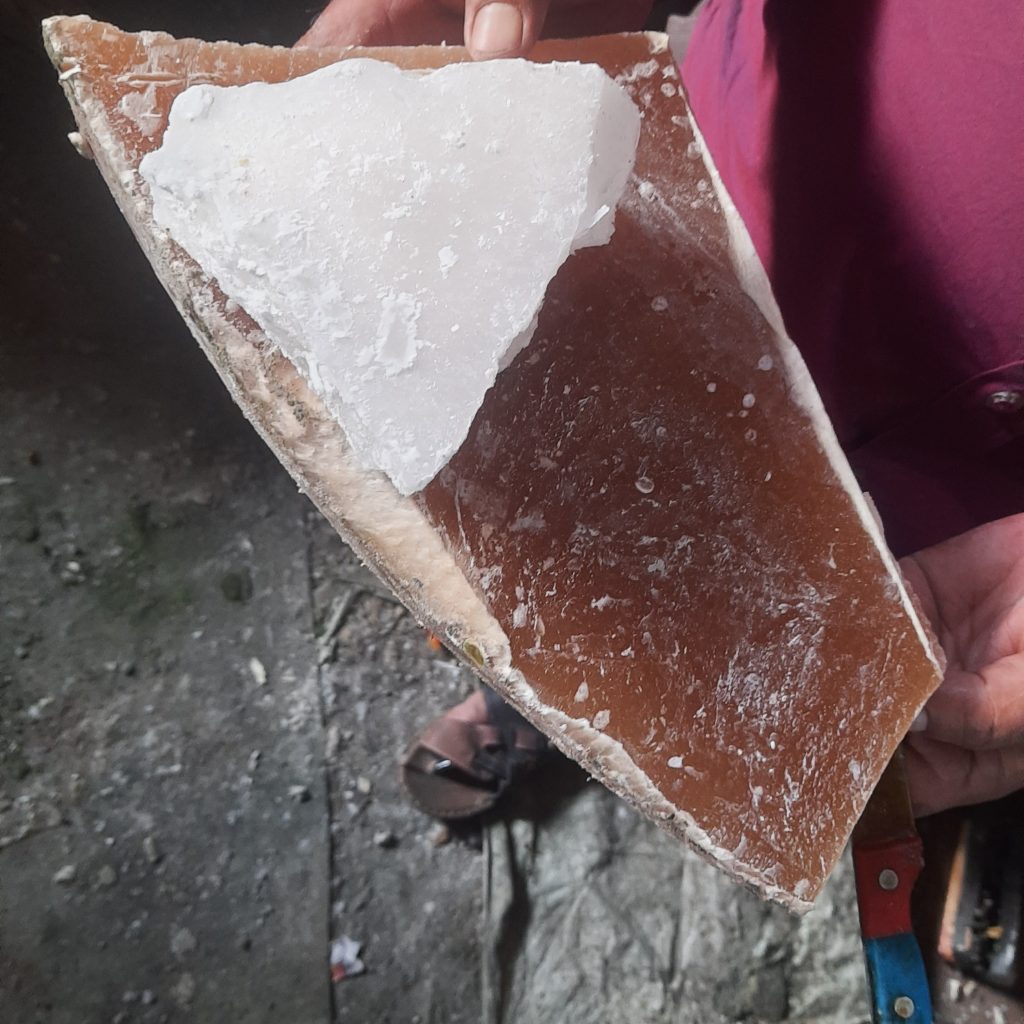
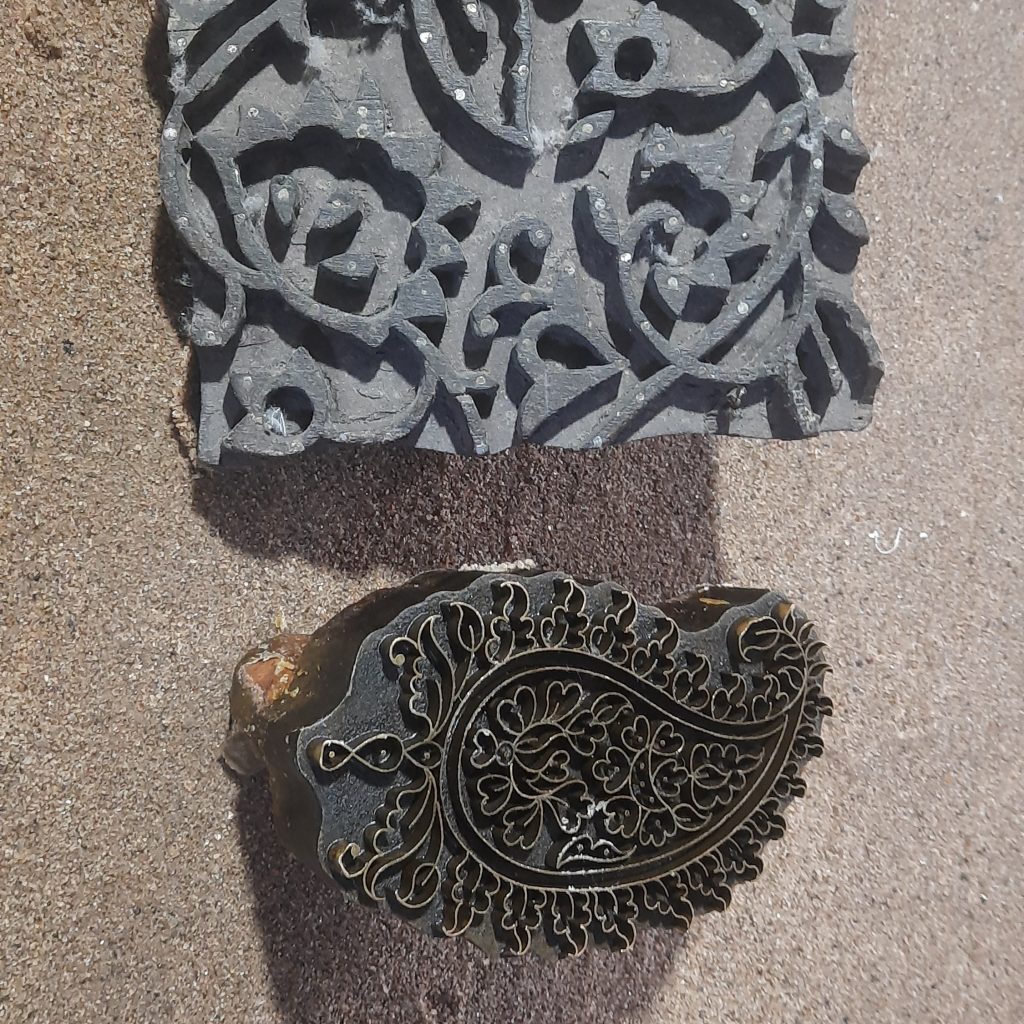

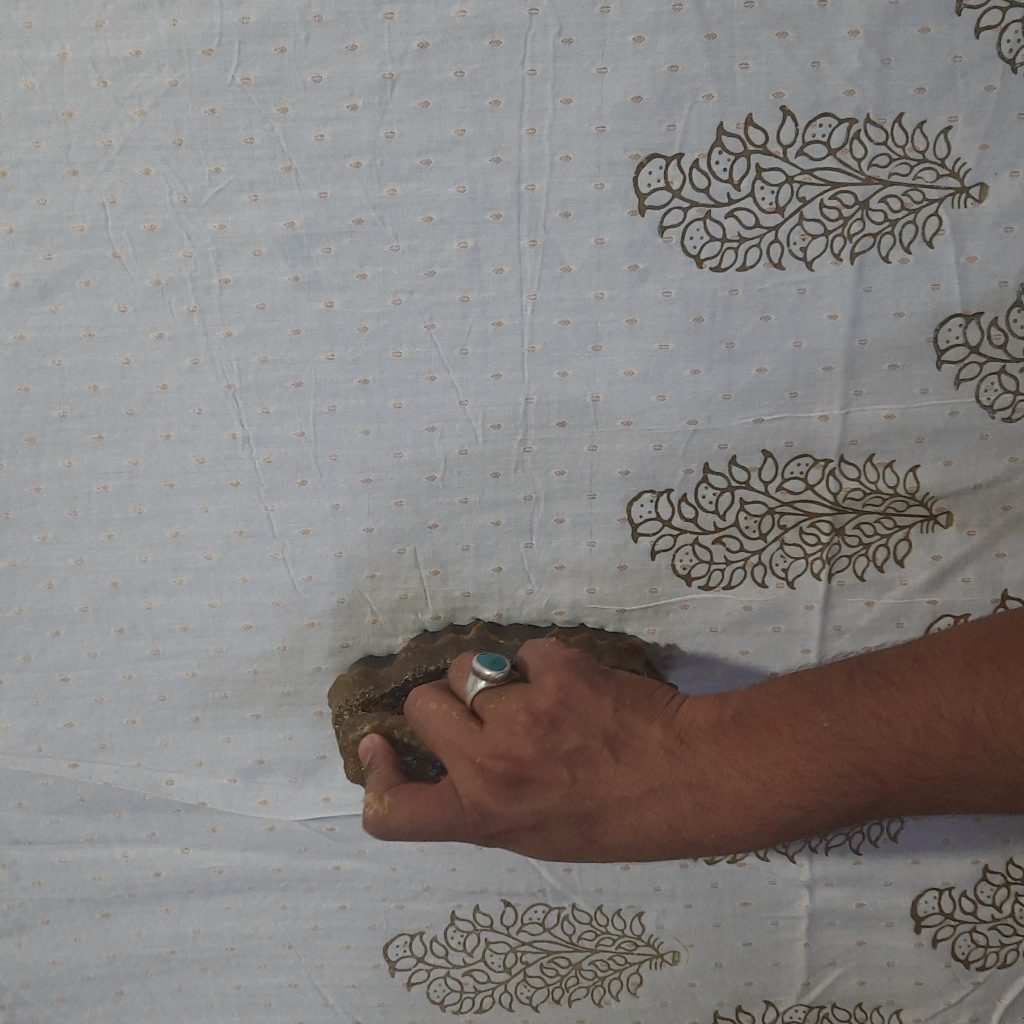
Dyeing
Once the fabric is imprinted with the wax and dried it is ready to be dyed. While the artform in its initial phases encouraged the use of natural dyes, acute competition lead to the promotion of chemical dyes to sustain in the modern day markets. The fabric is dipped in the required colour multiple times before being dried again. The design wax restricts the dye from absorption in the waxed area, thereby creating designs in the dyed fabric.
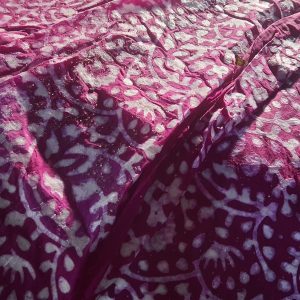
De-waxing
As can be seen in the image above, post dyeing and drying it is essential to remove the wax resin which remains imprinted on the fabric. The dyed fabric is dipped in boiling water, for multiple rounds until the fabric is free from the wax resin. The left over wax which gets collected in the boiling tank is strained out from the water, dried, processed and reused in the waxing process.
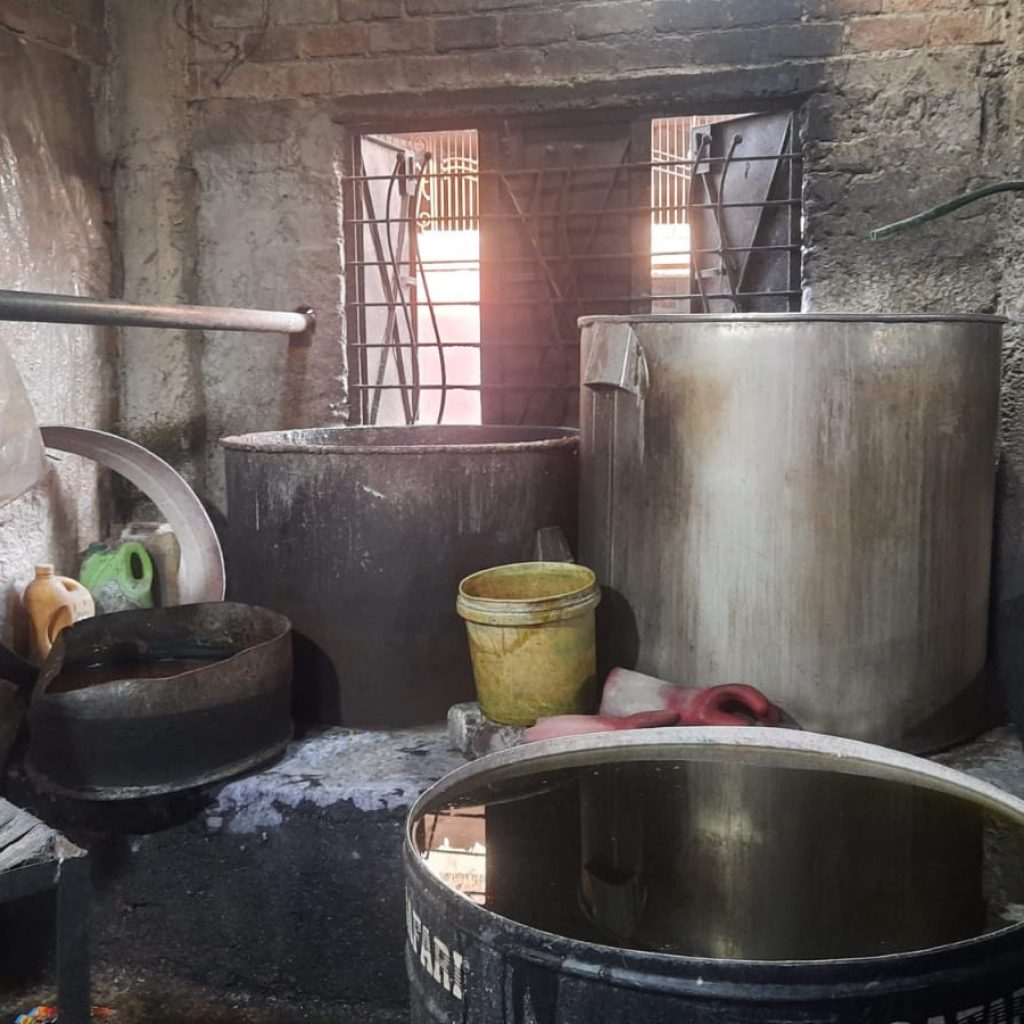
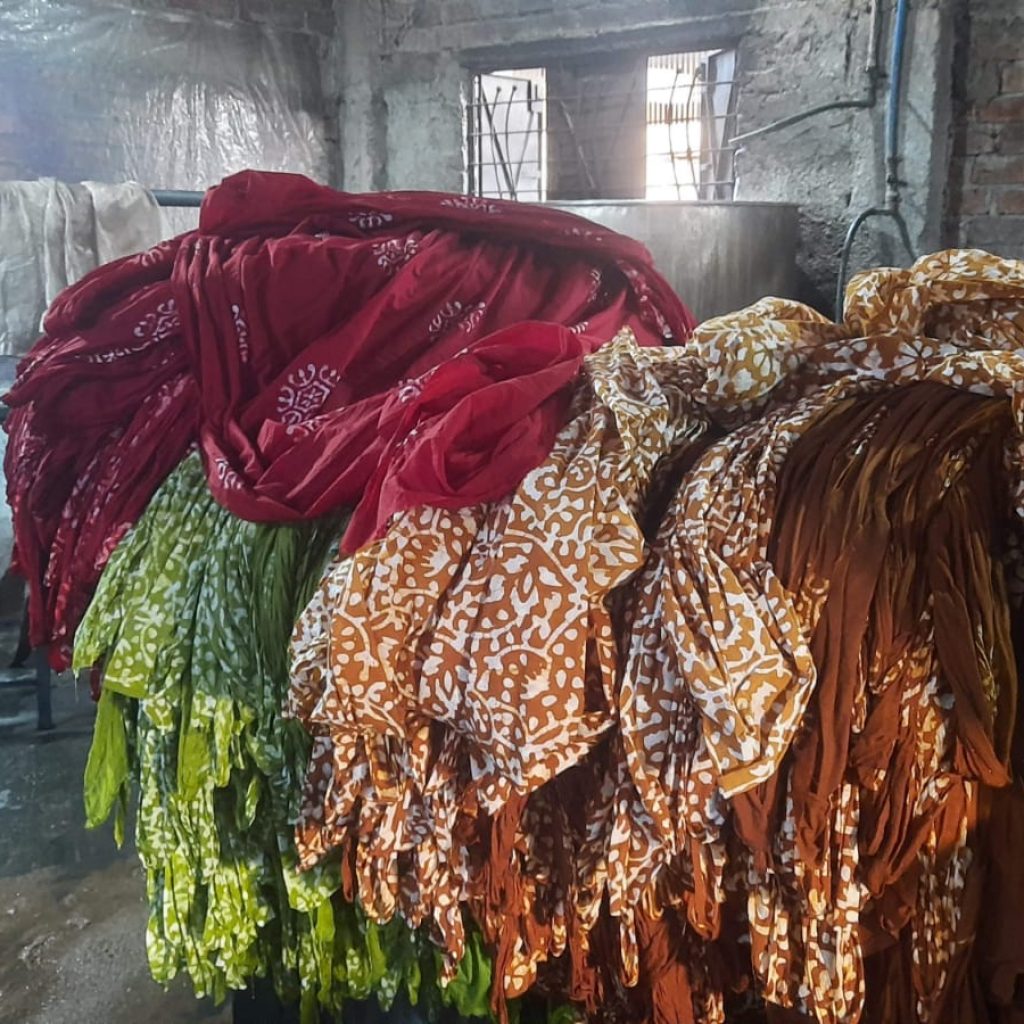
Rewaxing
If the designer wishes to add more shades of colour to the fabric, it is then rewaxed to repeat the process for other shades. The waxing-dyeing-drying-dewaxing process continues until all shades as required gets added to the fabric.

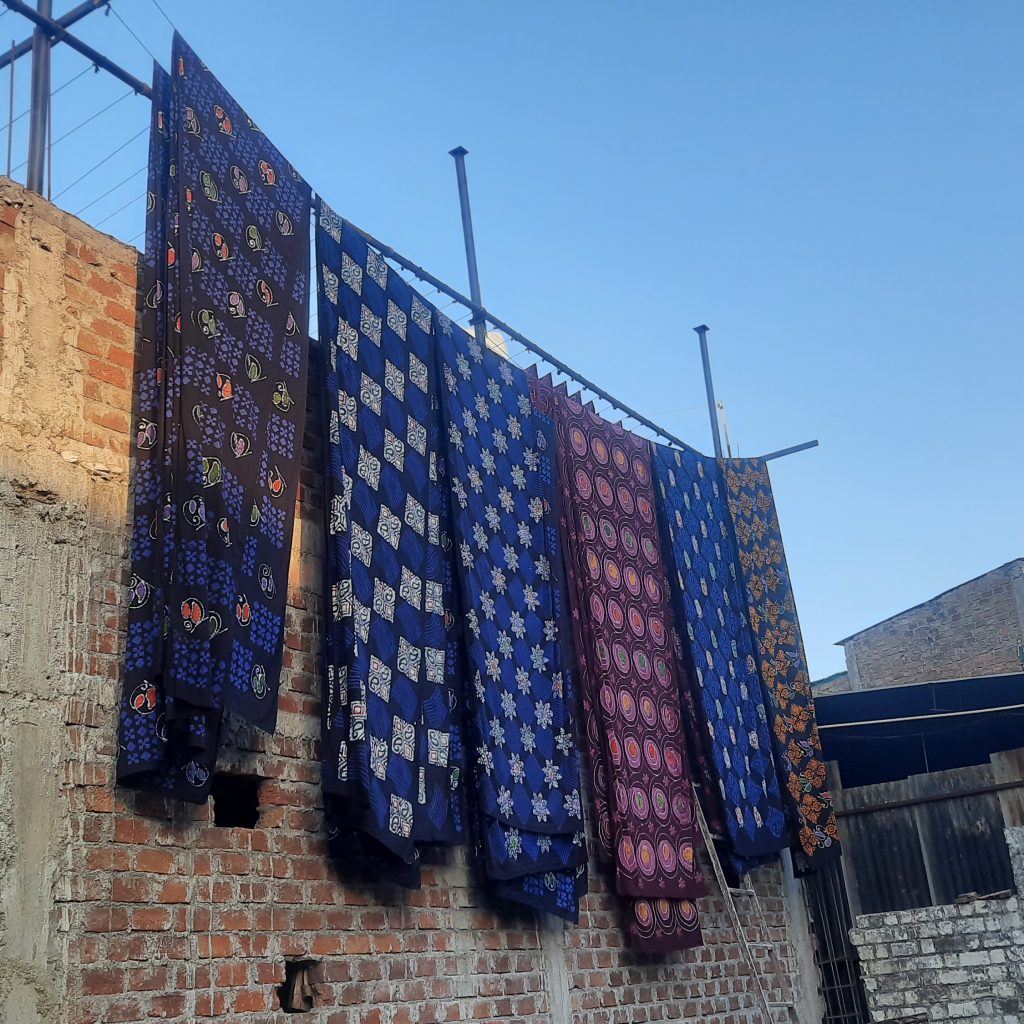
Washing and drying
This is the last leg of the process, where the dyed cloth is washed in normal water to fasten the colour on the fabric. It also helps clean the fabric from impurities if any. Once the washing is done the fabric reaches the dryers of the streets of Bherugarh where these beautifully designed fabric is left to sun-dry.
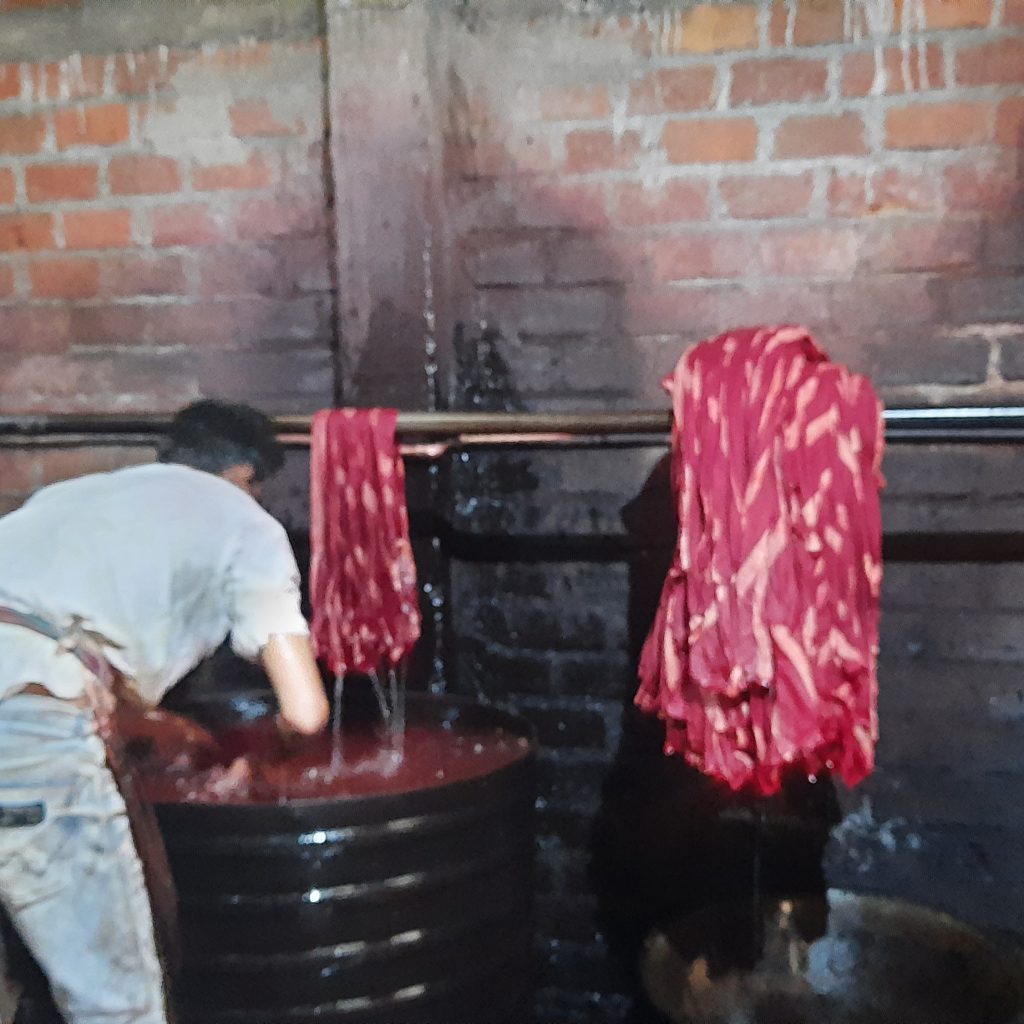
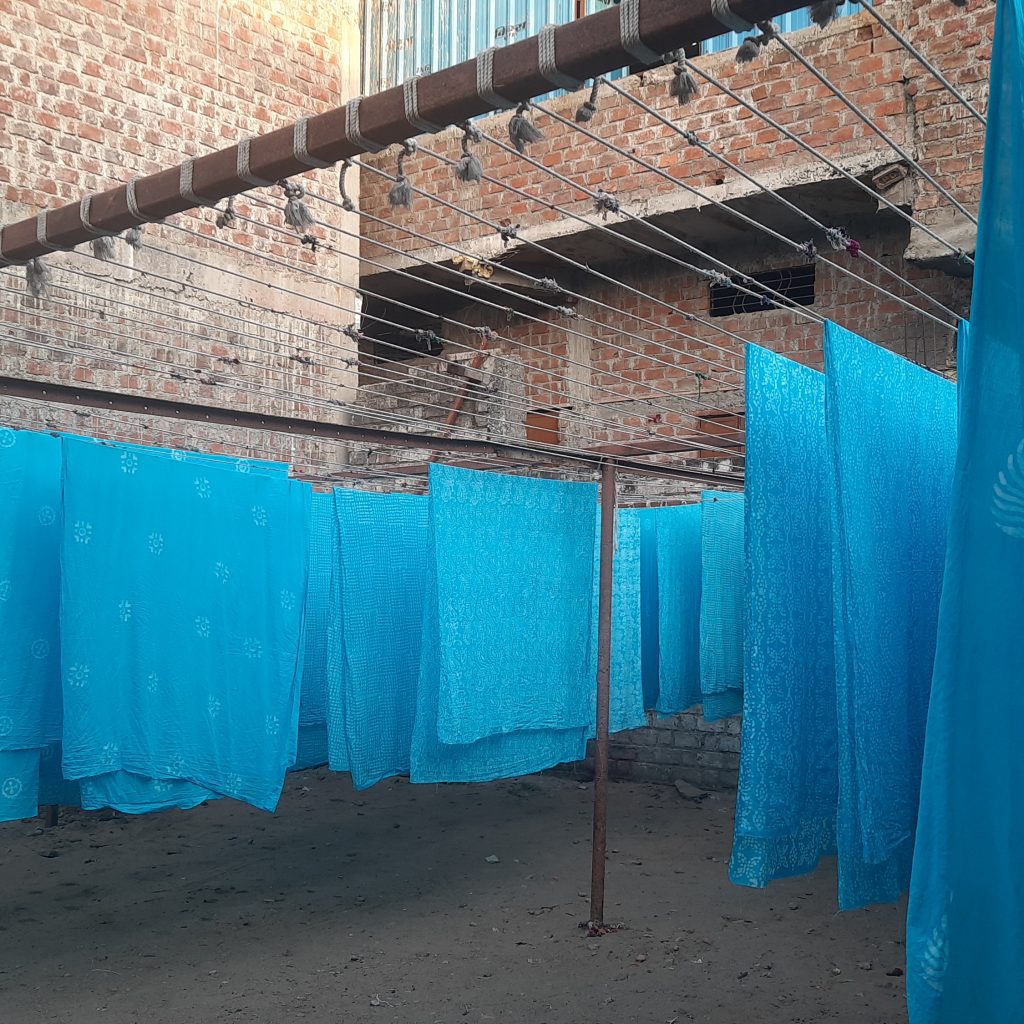
0 Comments